軸鍛件的加熱淬火和感應(yīng)淬火
文章出處:未知
人氣:
發(fā)表時間:2019-07-08 17:23
從80年代以來,首先開發(fā)應(yīng)用了支承輥工頻整體感應(yīng)加熱淬火工藝方法。軸鍛件的支承輥整體感應(yīng)加熱原理是以表面感生渦流加熱及表層熱量向內(nèi)部傳導(dǎo)加熱兩種方式共同進(jìn)行的。
軸鍛件的加熱的開始階段由于感生渦流的“集膚效應(yīng)”使表面迅速升溫,表面金屬一旦達(dá)到相變點以上便變?yōu)轫槾判?,渦流強(qiáng)度峰值逐漸向內(nèi)部尚未奧氏體化金屬的前沿推移,使奧氏體化層向內(nèi)部推進(jìn)延伸。因為支承輥要求奧氏體化層深較深,為避免表面過熱,在加熱后期階段,相當(dāng)程度上要借助于傳導(dǎo)方式向內(nèi)傳熱,***終達(dá)到預(yù)定的奧氏體化層深。
整體感應(yīng)加熱淬火裝置立式安裝,爐體下部有電機(jī)驅(qū)動裝置,支承輥被裝卡在上下***之間并由下***帶動旋轉(zhuǎn)。整體感應(yīng)器即為爐體,外部由金屬結(jié)構(gòu)支承,內(nèi)部感應(yīng)線圈由水冷銅管制成。內(nèi)表面粘貼隔熱材料。
總之軸鍛件整體感應(yīng)加熱淬火工藝有以下特點:
1.勞動條件好,便于自動控制。
2.中心部分溫升不大,殘余拉應(yīng)力很小,可以不加中心通孔。
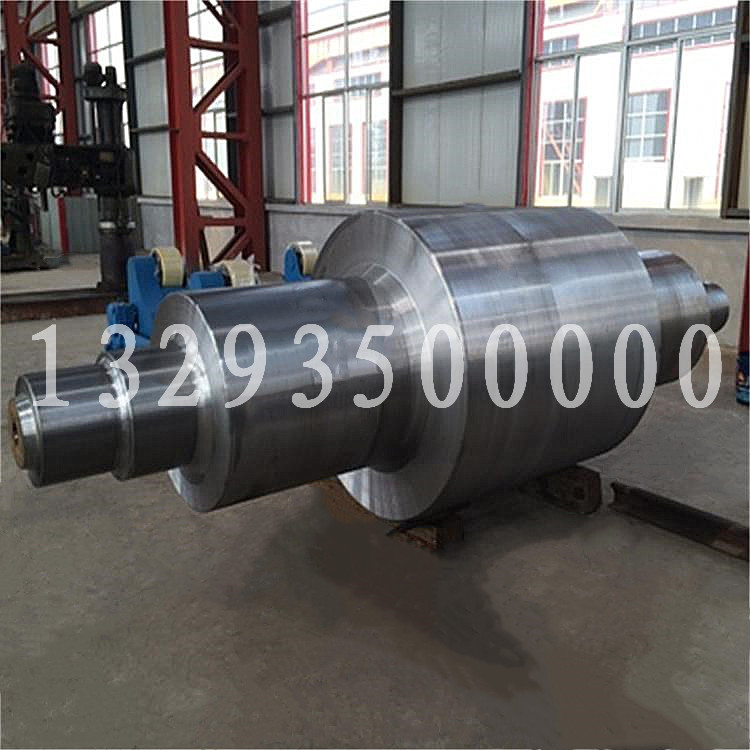
3.加熱溫度均勻,硬度均勻性可以達(dá)到的水平。
在連續(xù)式感應(yīng)加熱淬火工藝方法中有一類是用兩種不同頻率的感應(yīng)器相匹配進(jìn)行感應(yīng)加熱的工藝,在輥面溫度控制和加熱層溫度分布方面很有特點,稱為雙頻感應(yīng)淬火工藝。
感應(yīng)淬火操作是將整體預(yù)熱到220℃的冷軋工作輥裝卡到活動框架上,輥身下端面與工頻感應(yīng)器下平面保持在一個水平面上,兩個感應(yīng)器從送電到全部進(jìn)入輥身正常淬火,其功率分為五檔由小到大鑄件增加,直到淬火全功率。同樣,當(dāng)感應(yīng)器離開輥身上端面時,功率也分為五檔由大到小逐漸減小,直至全部離開輥身。

感應(yīng)加熱環(huán)節(jié)完成之后,為減小淬火應(yīng)力適當(dāng)預(yù)冷然后噴淬是必要的。由于軸鍛件奧氏體再高溫階段比較穩(wěn)定,噴水器與下感應(yīng)器之間有40mm的空隙,輥面空冷降溫到850℃左右的溫度,不會影響淬火硬度。
軸鍛件雙頻感應(yīng)淬火工藝的冷卻方式很有特點,輥身下拉進(jìn)入噴水器未知后,低壓大水量連續(xù)噴射冷卻7-10min,使淬硬層深度范圍內(nèi)以超過貝氏體臨界冷速的速度冷卻到馬氏體點以下,再改為浸水冷卻。
高硬度的冷軋工作輥回火溫度很低,殘余應(yīng)力相當(dāng)高。軸鍛件單頻感應(yīng)淬火的殘余拉應(yīng)力峰很大且靠近表面,整體淬火的殘余拉應(yīng)力峰仍很大但已推移到100mm深處。這種應(yīng)力分布是我們所希望的,它可以避免使用時與軋制工作應(yīng)力疊加,減少內(nèi)部疲勞剝落現(xiàn)象。